|
|
At Sonus International, we provide best ointment manufacturing machines, as per the client’s requirements. |
OPERATION SEQUENCE FOR OINTMENT/CREAM MFG. |
 |
Making sure body internals for works that are cleaned carefully |
 |
Charging of the pre-resolute Water quantity for Water phase vessel |
 |
Supply for steam as well as melting down sugar |
 |
Additions of the additives manually as well as mix at existing temperature |
 |
Charging of petroleum jelly / oil / wax to the oil phase vessels |
 |
Supply for heat and steam them |
 |
Vacuum transfer heated oil as well as heated water into ointment / cream |
 |
Starting Homogenizers for the dispersion and emulsification |
 |
After verification of ointment / cream discharge the product for storing tank through transfer pump |
 |
Keeping the product under slow speed ogitation in storage vessel |
 |
Product transferring to filling via material pump. |
|
|
Application |
 |
Pharmaceuticals: Gels, Creams, Biotech products, and Sterile and Non Sterile Ointments. |
|
Cosmetics: Hair Dye Creams, Cold Creams, Lotions, Gels, Conditioners, Shampoo, Toothpaste, and Mascara make-up. |
|
|
Technical Feature |
Main Vessel : |
 |
Especially Design drives assembly. |
 |
Homogenizer (alternative) – Top Entry, Bottom Entry, side Entry, with movement facility. |
 |
Hydraulic lid lift for easy and fast cleaning of the top vessel and dish |
 |
Loads Cell for accurate and fast measuring systems. |
 |
Option of different kinds of anchor designs. |
 |
Supple product transfer fitting and pipe for loading hydraulic and cell lifting. |
 |
VFD for the Anchor agitators for varying RPM. |
 |
VFD for the Homogenizer to differ RPM. |
|
|
Wax Vessel : |
 |
Open top having top Entry agitators Cowl disc kind or paddle through Slow Speed Anchors. |
 |
Close top through top/bottom entry agitators Cowl disc kind or propeller kind of stirrer. |
|
|
Water Vessel : |
 |
Open top through top entry propellers stirrer. |
 |
Close top through bottom or the top entry propellers. |
|
|
Common Feature |
|
The major functions of the ointment manufacturing machines are emulsifying and mixing. That in broader sense indicates producing extremely fine suspensions, emulsions, etc featuring outstanding homogeneity as well as thus lastly stability for mixed products. |
 |
Cleaning in the Place cycles through validation protocols. (Optional) |
 |
Electro polished Pipelines as well as joints are standard for the easy opening as well as re-fixing. |
|
Jackets having cooling and heating with the temperature control through Safety equipments. |
 |
No Human contamination / Air contamination. |
 |
Vacuum systems for transferring products through one vessel to another as well as zero retention with pre phase vessels as well as inter connecting pipelines. |
|
|
Control System |
|
Manual Control – Having temperature Timer / Indicator / Push Button / Single Phase protection for operating complete plant. |
|
Auto Control – PLC relied with the touch screen as well as password levels for feeding parameters of the procedure for / Stirrer timing / Heating / Stirrer speed / Cooling Homogenizer Timing / Vacuum / Pressure / Homogenizer speed etc. This alternative for the package to outfit requirement for every product. |
 |
Pre stored procedure parameter will assist in achieving constant product quality. |
 |
MMI (Touch Screen) to visualization of the machines of precise procedure data and condition |
|
PLC points out visualization of the Machine procedure data and condition, Alarm Signal, and Fault Message |
 |
SCADA package (optional) |
|
|
Design Base |
|
The special pharmaceutical designing permits application in the biotechnical procedure. The surface, material, and all-purpose designs are kept with GMP directives and recommendations of USFDA and FDA. |
 |
Vessel designs as per the ASME guidelines as well as tailor-made designs according to product / user’s Requirements. |
 |
All the vessels are according to GMP regulations. |
 |
Complete plant is designed as well as supplied according to CGMP guidelines. |
|
|
Advantages |
 |
Supple Configurations |
 |
Easy Operations |
 |
May Be Completely Automated |
 |
Integration into existing process control system |
 |
Fast product change over |
 |
Effective and fast cleaning CIP/SIP |
 |
Homogenous product steadiness without fascinated air bubbles. |
 |
Dispersing, mixing, and homogenizing with one operation |
|
|
Capacity |
5 Kg to 3000 Kgs. |
|
 |
Ointment Manufacturing Plant – Oil Phase / Wax Phase |
 |
Water Phase Vessel |
 |
Manufacturing Vessel |
 |
Storage Vessel |
 |
Oil Storage Tank |
 |
Inter connecting Piping and Valves |
 |
Homogenizer / Micronizer |
|
|
Automatic Tube Filling & Sealing Machine – Single Head/Double Head |
Sonus 35 –Single Head |
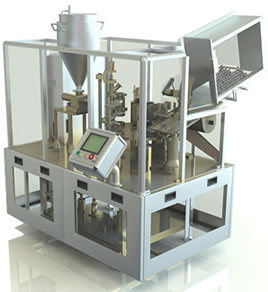 |
|
Product Overview |
SONUS 35 is the smallest tube filling machine in the range with capability of producing around 12,000+ tubes every shift. The tubes need to be manually transferred through tube box in cassette on machine. Often they are loaded individually into holders on turret. Firstly tubes are oriented and centered and after that filled. Then they are closed as per the kind of tubes. For metal tubes, they are crimped and flattened twice/ thrice. For plastic / laminate tubes, they initially are heated on inside periphery, and then sealed. Then batch details are coded on seal or crimp with the metal stereos as well as tubes are evicted out either to the collection containers or to the tube-transferring system for linking to downstream cartoner. |
|
Technical Specifications |
Features : |
 |
The pump inside ointment section has vertical dosing system that helps in easy suction. |
 |
We have combined bottom up filling and shut off nozzle together for accurate filling without any entrapment f air. |
 |
Index is highly smooth as required. |
|
You don’t have to adjust tools much and reproduction settings are also faster with less efforts and changeover. |
|
The other major highlighting of our ointment section are high quality sensors, safety measures, centralized lubrication, reversible tube, pressure drop tubes etc. |
|
|
Optional Equipment : |
 |
Filling in varied colors |
 |
Saddle fold |
 |
Plastic tube sealing |
 |
Gases flushed out before and after filling |
|
|
Sonus 150 – Double Head |
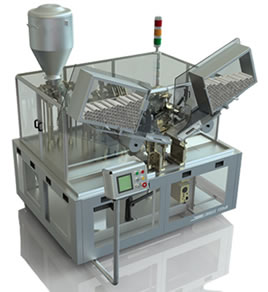 |
|
Product Overview |
SONUS 150 are the twin-head fast/medium speed tube fillers capable of producing around 45,000+ tubes every shift. The tubes need to be primary manually transferred through tube box in two cassettes for the ointment manufacturing machines. Then they are loaded individually into holders on turret. Firstly tubes are oriented and centered and after that filled. Then they are closed relying on the kind of tube. For metal tubes, tubes are crimped as well as flattened twice/thrice. For laminating/plastic tubes, first they are heated on inside periphery as well as then sealed. The batches details are coded on seal or crimp with the metal stereos as well as tubes are evicted out either to the collection containers or to the tube-transfer systems for linking to downstream cartoner. |
|
Technical Specifications |
Features : |
 |
The pump unit has a vertical dosing system, which aids in easy suction |
 |
Bottom-up filling coupled with shut-off nozzle ensures accurate & clean fill without air entrapment |
 |
Indexer is absolutely smooth. |
|
Tool-less adjustment coupled with quicker reproduction of the settings (aided through the position indicators as well as tri-clover fittings) create changeover very easily. |
|
Product level sensors, centralized lubrications, as well as host for the safety features including detection of the jammed tube, reverse tube, air pressure drops etc. are element of the basic ointment manufacturing machines. |
|
|
Optional Equipment : |
|
Contact us for all your ointment manufacturing machines requirements. |
|
|
|